Four new sustainable building materials to watch
- Georgia Starkey
- Mar 15, 2021
- 3 min read
Updated: Oct 12, 2021
With the need for better buildings more urgent than ever, great minds across Australia are finding innovative ways to reshape the building sector with sustainable construction material
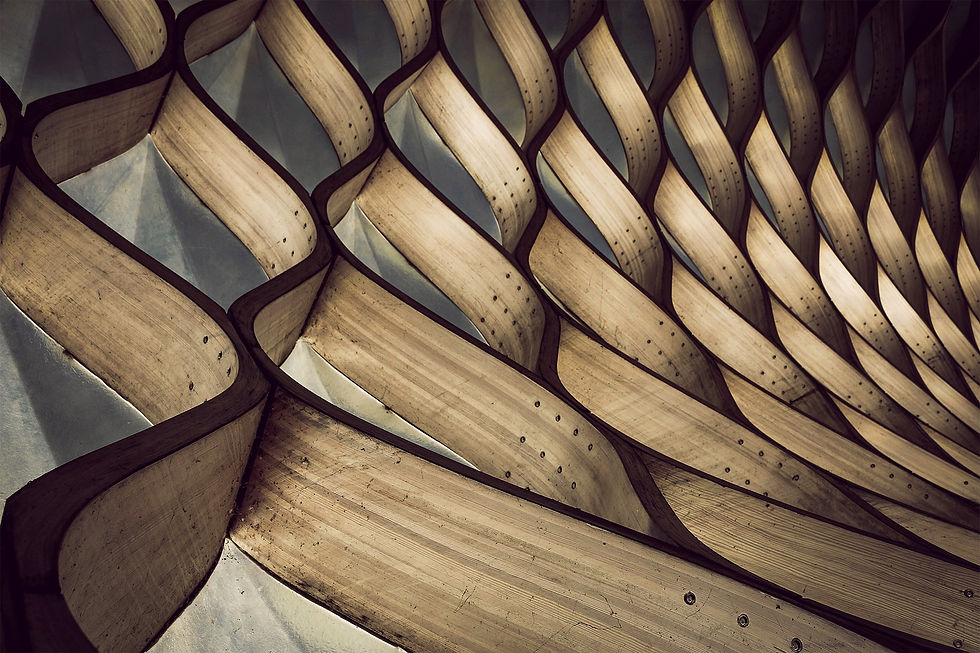
When it comes to rethinking sustainability, the Australian building sector is going to have to start from the ground up.
Australia’s construction sector is the fourth largest indirect emitter thanks to embodied carbon — the amount of carbon that goes into a building — with concrete and steel as two of its biggest offenders.
Not only are they carbon and energy intensive to produce; construction materials are difficult to recycle and contribute to the nation’s growing waste problem.
Thankfully, researchers are discovering new ways to revolutionise and rebuild a more sustainable building sector, brick by recyclable brick.
“Smartwood” from recycled timber
Australian company 3RT and researchers at Flinders University have spent the past six years perfecting a new type of “smartwood” out of recycled timber chips.
“Smartwood” combines a water based nano glue with waste wood that would otherwise be woodchipped to replicate the properties of natural hardwood so that it is comparable to that of a 100 year old tree.
So far, 3RT and Flinders researchers have already developed specialised recipes for over 100 wood types, including 30 international species, and are researching ways to achieve water, fire and termite resistance without any of the harmful ingredients.
Last week, the company announced its partnership with Bosch, one of the world’s leading manufacturing companies, to license the material overseas and boost “smartwood” technology on a global scale.
“We’re pretty ambitious – we’re talking about putting 10, 20, 30 units around the world in the next 5 to 10 years,” 3RT managing director Peter Toreele said.
Recyclable plastic bricks
Australian researchers are testing a new rubber polymer that can create construction materials out of recycled plastic waste.
The polymer, a mixture of sulfur and canola oil, forms a rubber material that can be stretched and compressed without melting, a process called “reactive compression molding.”
As a result, the powdered rubber can be compressed and heated with sustainable fillers such as recycled PVC, plant fibers or sand and shaped into bricks, tubings, rubber coatings and bumpers as an alternative to concrete.
“This new recycling method and new composites are an important step forward in making sustainable construction materials, and the rubber material can be repeatedly ground up and recycled,” lead author Flinders PhD Nic Lundquist said.
With few ways to recycle old PVC or carbon fibre, these bricks offer another potential route to create a more circular economy within the construction sector.
Archimats
Researchers at Monash University are pioneering a new recyclable building material that stands to revolutionise manufacturing and construction as we know it.
Archimats — short for “architectured” materials — are part of an emerging field of materials designed with an interlocked internal architectural structure to enhance properties including strength, durability, thermal insulation and energy absorption. This means archimats can expand the design possibilities beyond composite materials such as steel or concrete.
Researchers say archimats could reduce emissions from heavy concrete use, rebuild homes in disaster affected areas, boost micro manufacturing in smart technology and become vital in outer space construction.
Archimats are also almost entirely recyclable, easy to assemble and disassemble thanks to their structure.
Project leader Professor Yuri Estrin described it as “smarter, safer and more sustainable materials for use in manufacturing and industrial design.”
Green steel, thanks to renewables
With Australia making large investments into renewable hydrogen, experts are looking into the nation’s potential role in the green steel industry.
Green steel is created using hydrogen instead of metallurgical coal, reducing the amount of iron ore needed and cutting greenhouse gas emissions.
The process can be made even more sustainable by renewably generating hydrogen using Australia’s abundant wind and solar resources.
A report from the Grattan Institute found that capitalising on renewably powered hydrogen steelmaking could net Australia $65 billion in revenue and create 25,000 jobs in Queensland and New South Wales.
Green steel is already showing promise overseas with HYBRIT — a joint venture between Swedish companies SSAB, LKAB and Vattenfall — set to open its pilot plant within the year.
Comments